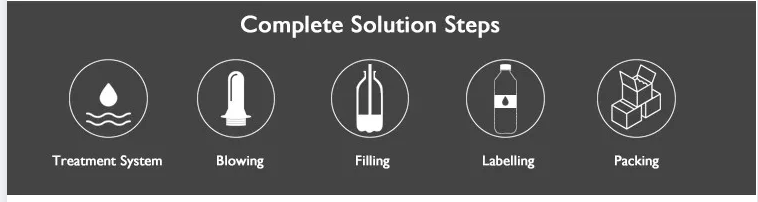
Product Description
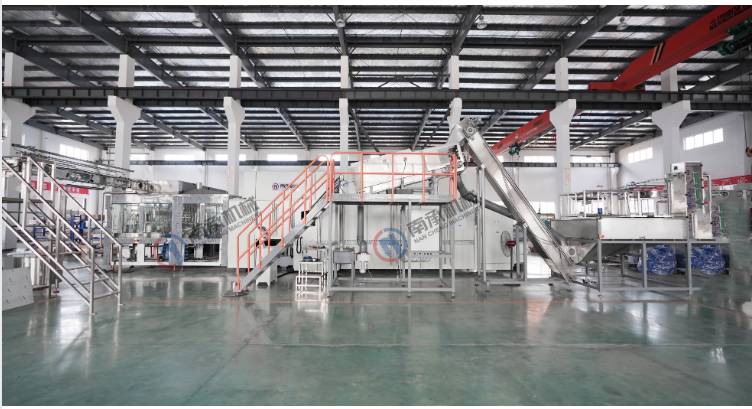
This combiblock consists of blowing unit, filling unit, and capping unit. With the synthetic application of electricity, mechanics, and pneumatics, and synchro controlled by servo system, Combi is applicable for the integrated control of several equipment and the whole production process.
It doesn't need empty bottle conveyor and rinsing part of the traditional filling machine, which saves a lot of room for the production plant, reduces water consumption from rinsing and energy consumption from fans used on empty bottle conveyor. It cuts a majority part of transit and guarantees the overall hygiene standard of the entire machine, which better helps end users increasing the overall production efficiency, lowering investment costs, saving energy consumption and maintenance costs.
Details Images
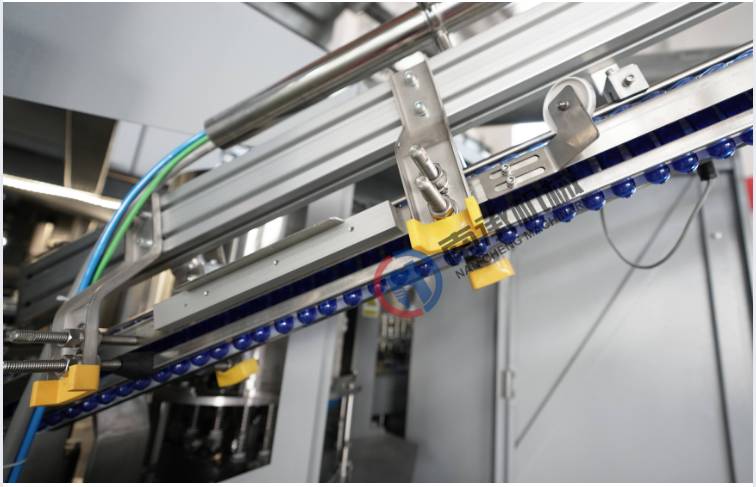
1. Preform feed-in and unscrambling
It adopts the matured worldwide-standardized way of preform feed-in and unscrambling, in which preforms go through preform elevator and are transmitted to preform unscrambler. Inside the preform unscrambler, preforms are automatically sorted and delivered by two inclined revolving cylinders with same speed, and the remaining ones will be picked by star wheel and sent back to preform hopper. The whole process of preform unscrambling is fully automatic and has high efficiency without preform scratches.
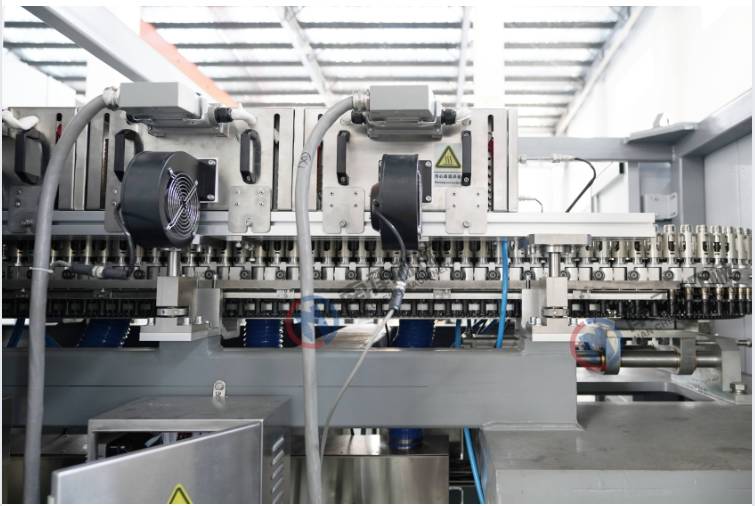
2. Heater
It adopts the matured worldwide-standardized way of preform feed-in and unscrambling, in which preforms go through preform elevator and are transmitted to preform unscrambler. Inside the preform unscrambler, preforms are automatically sorted and delivered by two inclined revolving cylinders with same speed, and the remaining ones will be picked by star wheel and sent back to preform hopper. The whole process of preform unscrambling is fully automatic and has high efficiency without preform scratches
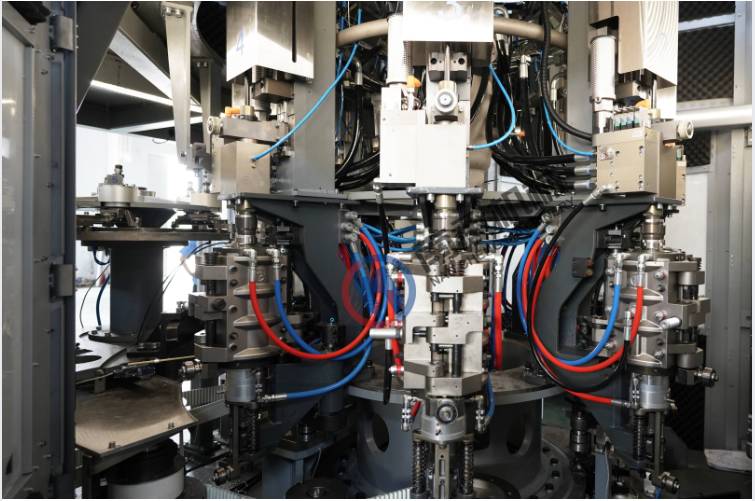
3. Blowing unit
Special manipulator delivers heated preforms to moulds along certain cam curve. After stretch pre-blow, the preform will be blown to bottles by connecting high pressure compressed air. Special manipulator sends the finished bottle out along certain cam curve.

4. Filling unit
The blow-made bottles are transported to filler via starwheel. After entering filler, the bottle is held by gripper of lifting
cylinder and realizes up and down under effect of cam.
The filler adopts gravity filling way. Bottle mouth rises to open filling valves and start filling. While product rises and plugs up air return hole, the filling will be finished. After filling, bottle mouth moves down and leaves the filling valve.
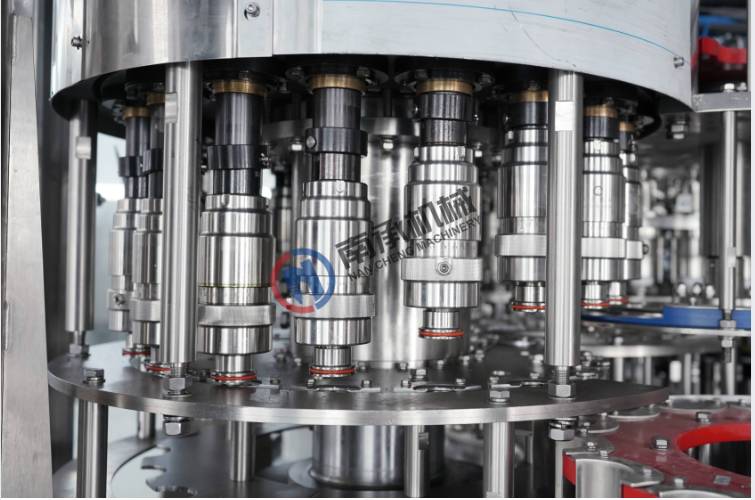
5. Capping unit
Bottles enter capper via transition starwheel. The anti-rotation knife of capper blocks bottle neck to keep bottle vertical and prevent rotation. Capping heads keep revolution and do rotation. Under effect of cam, the action of gripping cap, sleeve cap,screwing cap and discharging cap to finish the whole capping course. The finished bottles are conveyed via bottle-out starwheel onto bottle-out conveyor, and then are sent out of the combiblock. The whole machine adopts console sealing windows, beautiful and decent.
Raelated products
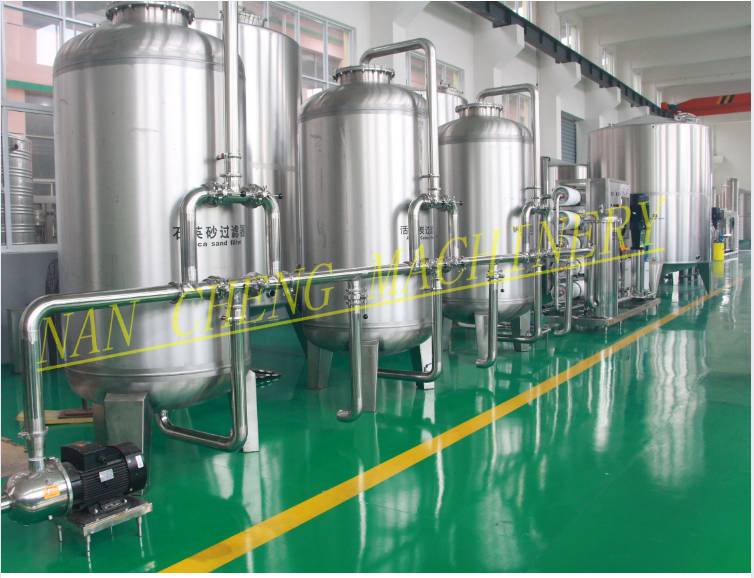
1-Water Treatment.
1 Raw water tank + Raw water pump
2 Silica sand filter + Active carbon filter + Sodium ion exchanger + Precision filter + Security filter
3 Reverse Osmosis (one level)
4 UV sterilizer
5 Finished water tank + Pure water pump
Benefits.
1/Stainless steel high pressure film shell
2/All kinds of capacity indicator, pressure indicator, electricity magnetic valve, balance device and pipe valve system
3/Online type pressure auto self-protection device
4/Online type electricity indicator (with stable compensation)
5/System safe protecting and alarm system
6/System frame
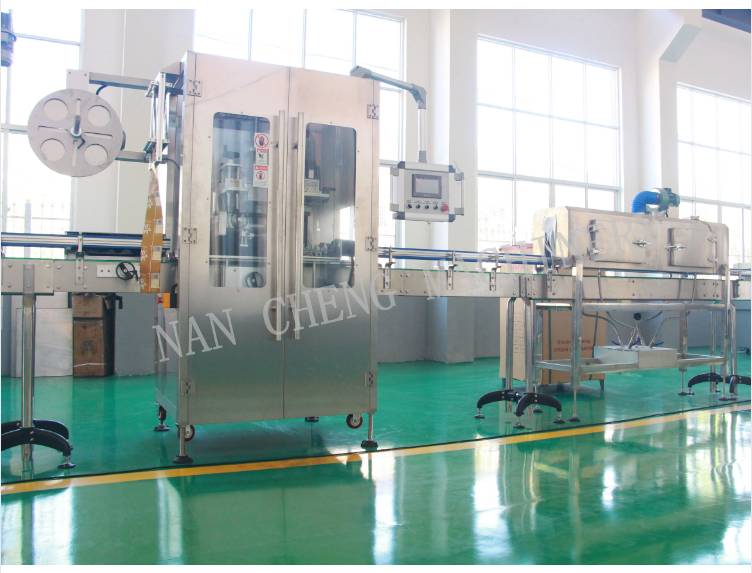
2-Labeling Machine.
Boasting four carousel sizes, up to three labeling stations and 24 configurations, can generate outputs of up to 72,000 containers per hour, when standalone, at an efficiency rate of 98%.
Benefits
1 / Greater performance and ergonomics
2 / Boasted production uptime
3 / Sustainable and quality production
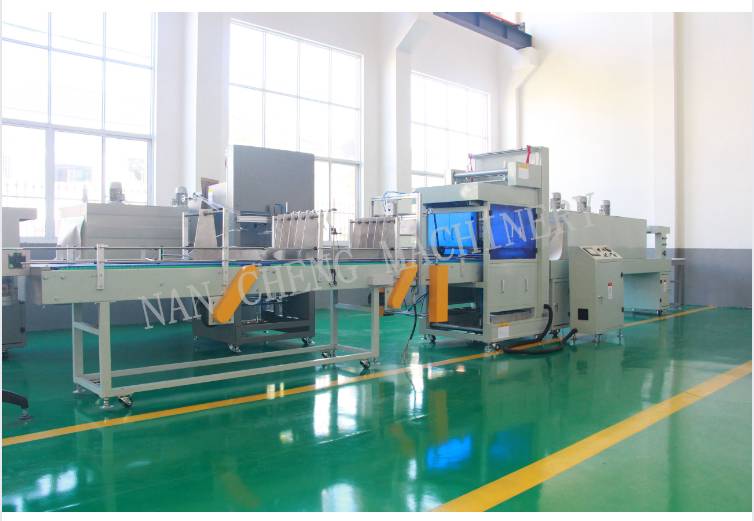
3-Packing Machine.
Once your beverage product has been filled and the bottle has been labelled, the primary package is gently transferred using conveyors to its secondary packaging process. The final result is the package the customer sees at the point of sale, so it needs to grab their attention. These packs ensure protection from elements such as weather, pressure and temperature changes. Whether you choose shrink-printed film, nested packs or wraparound cartons, King Machine packers gently feed bottles to ensure durable and cost-effective packs.
Benefits.
1 / Pack consistency and quality
2 / Gentle and precise infeed configuration
3 / Flexible handling of multiple SKUs
4 / Automatic pack and raw material changeovers
5 / Heat, glue, carton and film optimisation
Why choose NanCheng Blowing-filling-capping Combiblock
1) Special designed secondary blowing system monitors in time pressure curve of bottle stretch process in each cavity to provide accurate and timely parameters for technical adjustment, which is more convenient for operators to adjust technical parameters.
2) Adopt manipulator transfer technology that cam mechanism has precise control. Catch and send preforms at high speed and the quality is reliable. Taking preform, sending preform, taking bottle and sending bottle match action of opening and closing mould to ensure that the movement process is exact and high efficient. Taking preform, sending preform, taking bottle and ranking bottle are finished automatically by manipulator, avoiding middle pollution.
3) The cam mechanism controls exactly opening and closing of mould frame. Special mould locking and pressurizing system and simple and firm mould frame structure can control independently the blowing parameters of each cavity. Good malfunction diagnosis function and special blowing structure ensure the sealing reliability under various pressure. The blowing pressure can be adjusted.
4) Stretch rod control exactly preform's axial stretch. The first blow and second blow control preform's vertical stretch. By
precise adjustment of the first and second blow, the ideal distribution of bottle wall thickness can be achieved.
5) Break conventional design and adopt structure of coaxial rotary bushing with small cubage and light weight. Adopt two deep groove ball bearings to fix two ends to make outside sleeve and core axes concentric, to ensure that the rotary sealing ring is not easy to be damaged. At the same time, increase one water back channel to make the leakage water in Gore circle flows back along pipe, ensuring that the water distributor won't have leakage.
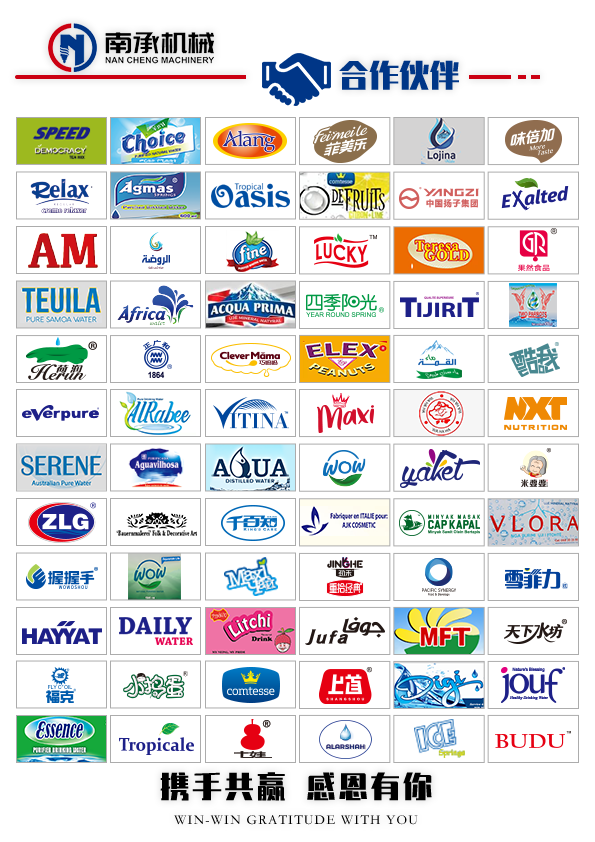
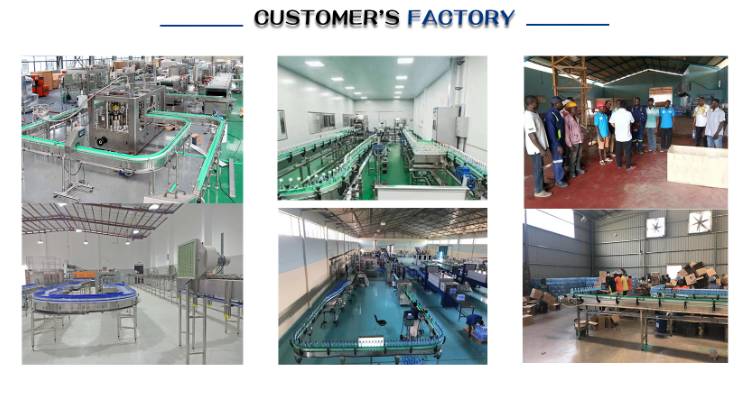
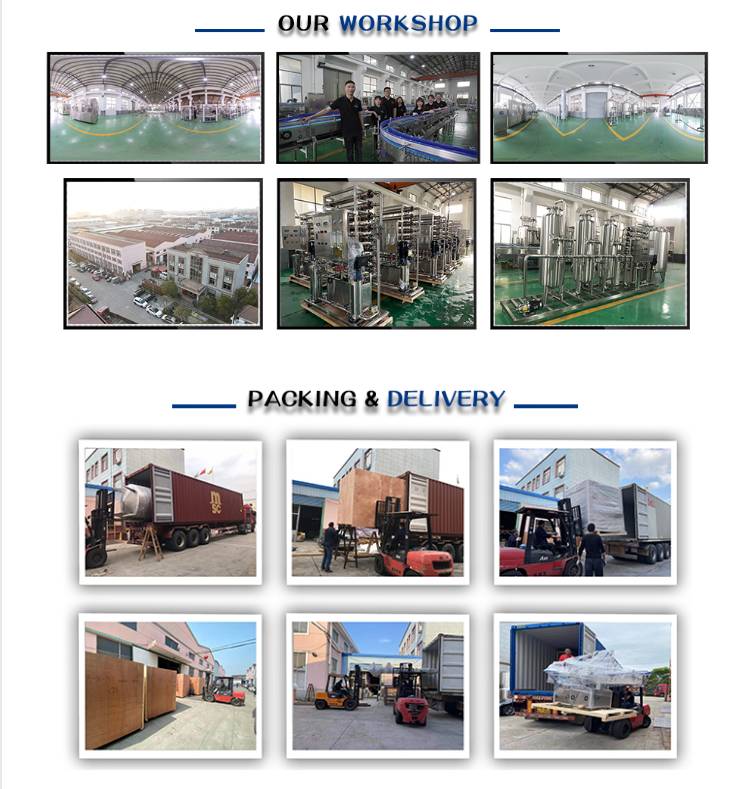
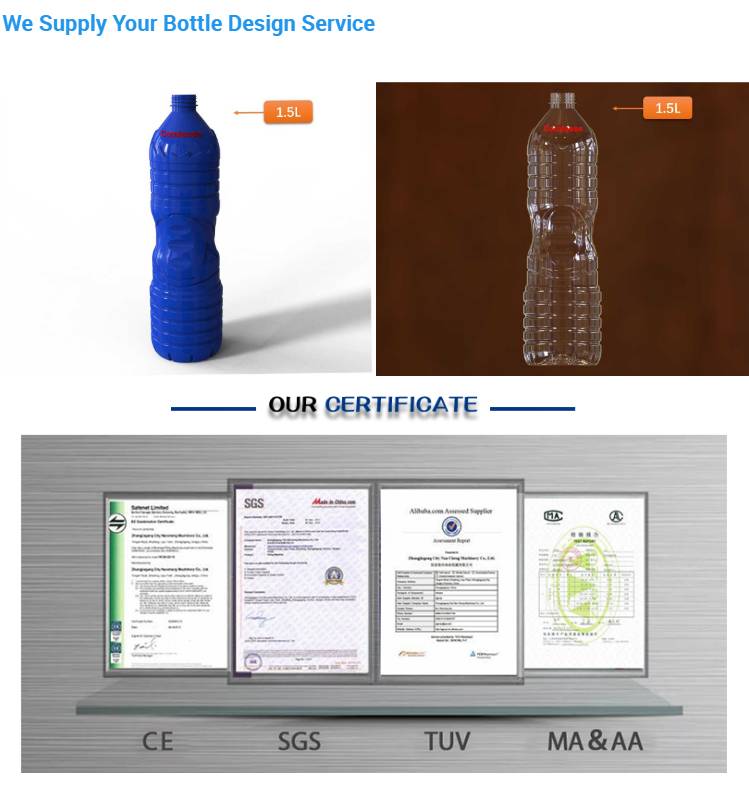
FAQ
Q1:Do you have any reference project?
>> A1:We have reference project in most countries, and you can visit their factories if we get the permission of the customer.
Q2:What's your guarantee or the warranty of the quality if we buy your machines?
>>A2:We offer you high quality machines with 2 years guarantee . we will give u spare part free in 2 years.
Q3: Do you provide customized service?
>> A3: We will customize the machine according to your needs, materil ,power,filling type,the kinds of the bottles and so on.
Q4:When can I get my machine after I paid?
>> A4:We will deliver the machines on time as the date we agreed both side.
Q5:How can I install my machine when it arrives?
>> A5:We will send our engineer to your side as soon as you get all your machines ready, for testing and teaching your technicians how to run the machines.